Description
Tungsten Carbide Copper Milling Inserts, also known as scalping cutter for copper and copper alloy.
Our cutting blade showcases exceptional material removal performance, facilitating efficient and rapid milling of copper surfaces to elevate processing efficiency. Tailored for applications demanding precision, it excels in ensuring post-processing smoothness and accuracy on copper surfaces. With remarkable wear-resistant properties, this blade significantly extends its lifespan, reducing the need for frequent replacements and thereby enhancing overall production efficiency. Designed with a focus on minimizing cutting resistance, it effectively reduces resistance during cutting, limits heat accumulation in the machining process, contributing to an extended tool and workpiece lifespan.
In addition, our specialized tool is designed for the removal of oxidized scales and defects from the surfaces of copper and copper alloy strips after undergoing hot mill processes. This tool is dedicated to continuous roughing of both up and down sides of thin copper and copper alloy boards rolled in a hot situation. Ideal for applications in electronic equipment, such as connector terminals or lead frame materials, our scalping cutter is engineered to handle even high-strength and difficult-to-cut copper alloys. With high-strength cemented carbide and excellent brazing technology, it not only scalps the surface effectively but also contributes to significant productivity improvements for our customers.
This blade possesses outstanding material removal performance, enabling efficient and rapid milling of copper surfaces to enhance processing efficiency. The blade excels in precision cutting, ensuring the smoothness and accuracy of the copper surface post-processing, making it suitable for applications with high demands on processing quality. With remarkable wear-resistant properties, the blade extends its lifespan, reducing the frequency of replacements and thereby increasing overall production efficiency. The blade's design factors in cutting resistance, effectively reducing resistance during cutting, minimizing heat accumulation in the machining process, and contributing to prolonged tool and workpiece lifespan.



Grade List
Grade | ISO Code | Physical Mechanical Properties (≥) | Application | ||
Density g/cm3 | Hardness(HRA) | T.R.S N/mm2 | |||
YG3X | K05 | 15.0-15.4 | ≥91.5 | ≥1180 | Suitable for precision machining of cast iron and non-ferrous metals. |
YG3 | K05 | 15.0-15.4 | ≥90.5 | ≥1180 | |
YG6X | K10 | 14.8-15.1 | ≥91 | ≥1420 | Suitable for precision machining and semi-finishing of cast iron and non-ferrous metals, as well as for processing of manganese steel and quenched steel. |
YG6A | K10 | 14.7-15.1 | ≥91.5 | ≥1370 | |
YG6 | K20 | 14.7-15.1 | ≥89.5 | ≥1520 | Suitable for semi-finishing and rough machining of cast iron and light alloys, and can also be used for rough machining of cast iron and low alloy steel. |
YG8N | K20 | 14.5-14.9 | ≥89.5 | ≥1500 | |
YG8 | K20 | 14.6-14.9 | ≥89 | ≥1670 | |
YG8C | K30 | 14.5-14.9 | ≥88 | ≥1710 | Suitable for inlaying rotary impact rock drilling and rotary impact rock drilling bits. |
YG11C | K40 | 14.0-14.4 | ≥86.5 | ≥2060 | Suitable for inlaying chisel-shaped or conical teeth bits for heavy-duty rock drilling machines to tackle hard rock formations. |
YG15 | K30 | 13.9-14.2 | ≥86.5 | ≥2020 | Suitable for tensile testing of steel bars and steel pipes under high compression ratios. |
YG20 | K30 | 13.4-13.8 | ≥85 | ≥2450 | Suitable for making stamping dies. |
YG20C | K40 | 13.4-13.8 | ≥82 | ≥2260 | Suitable for making cold stamping and cold pressing dies for industries such as standard parts, bearings, tools, etc. |
YW1 | M10 | 12.7-13.5 | ≥91.5 | ≥1180 | Suitable for precision machining and semi-finishing of stainless steel and general alloy steel. |
YW2 | M20 | 12.5-13.2 | ≥90.5 | ≥1350 | Suitable for semi-finishing of stainless steel and low alloy steel. |
YS8 | M05 | 13.9-14.2 | ≥92.5 | ≥1620 | Suitable for precision machining of iron-based, nickel-based high-temperature alloys, and high-strength steel. |
YT5 | P30 | 12.5-13.2 | ≥89.5 | ≥1430 | Suitable for heavy-duty cutting of steel and cast iron. |
YT15 | P10 | 11.1-11.6 | ≥91 | ≥1180 | Suitable for precision machining and semi-finishing of steel and cast iron. |
YT14 | P20 | 11.2-11.8 | ≥90.5 | ≥1270 | Suitable for precision machining and semi-finishing of steel and cast iron, with moderate feed rate. YS25 is specially designed for milling operations on steel and cast iron. |
YC45 | P40/P50 | 12.5-12.9 | ≥90 | ≥2000 | Suitable for heavy-duty cutting tools, providing excellent results in rough turning of castings and various steel forgings. |
YK20 | K20 | 14.3-14.6 | ≥86 | ≥2250 | Suitable for inlaying rotary impact rock drilling bits and drilling in hard and relatively hard rock formations. |
Order Process

Production Process
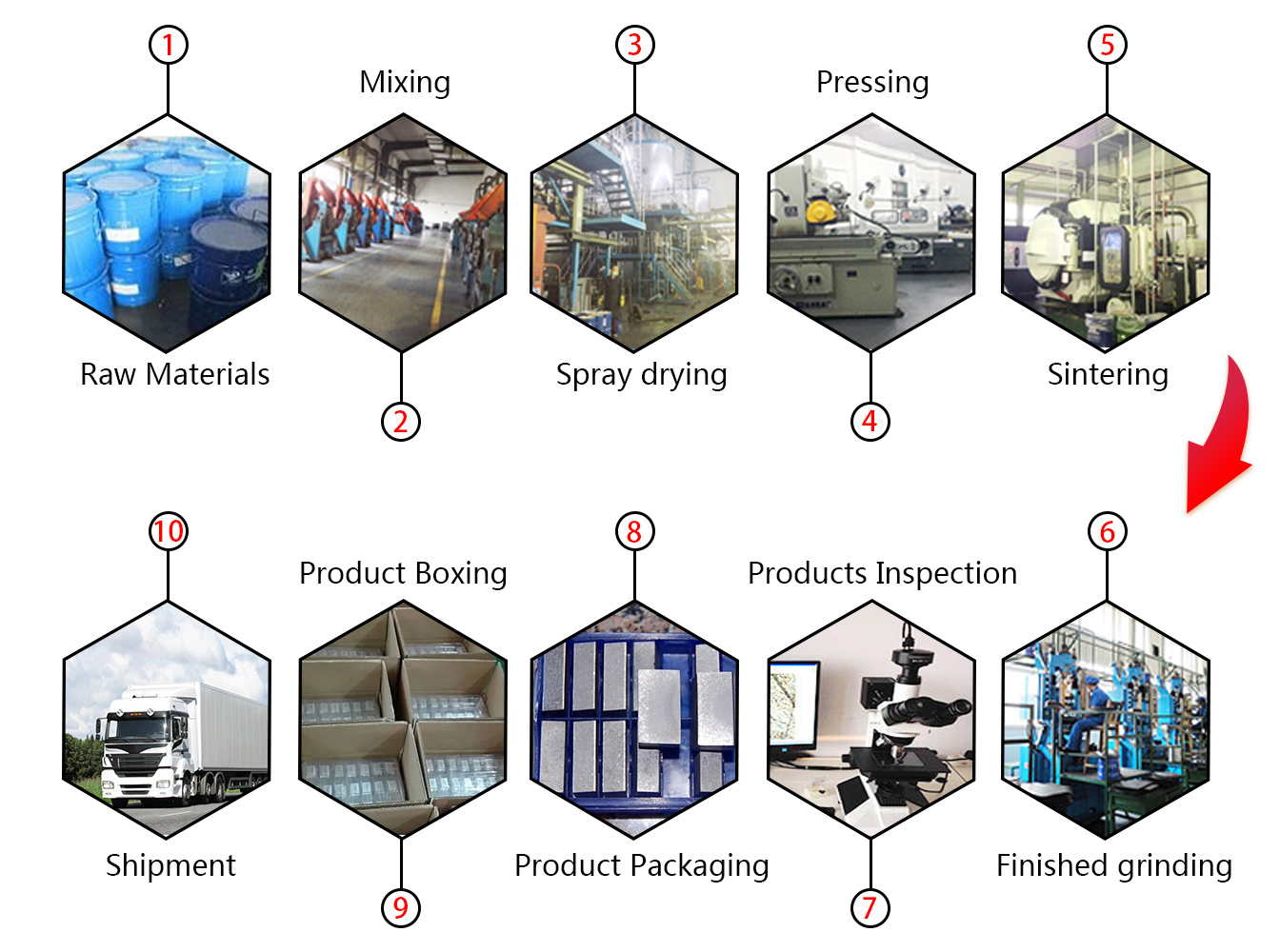
Packaging
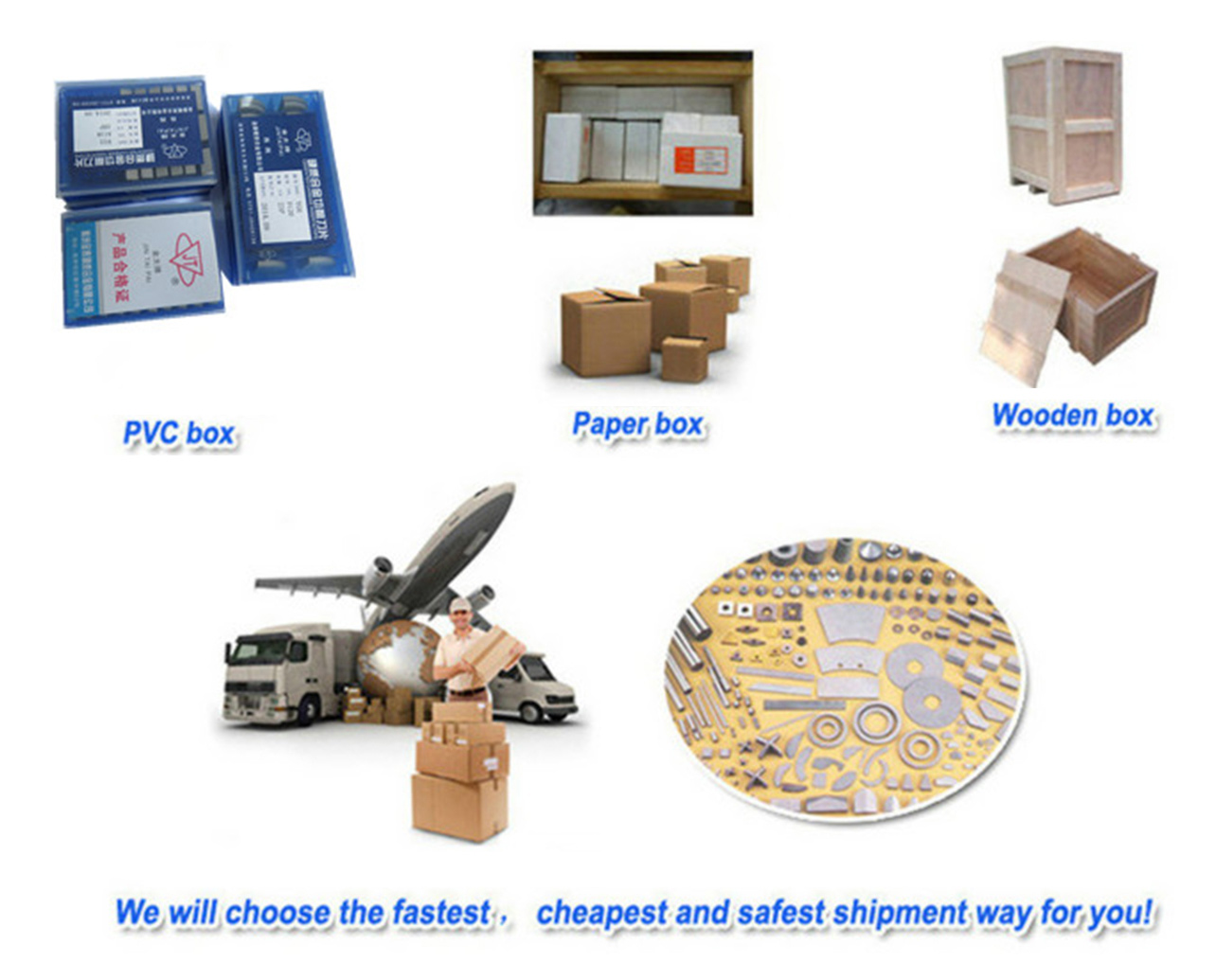