Description
Product Application
Such as: precision parts punching, stretching, precision bearings, instruments, meters, pens, spraying machines, water pumps, machinery fittings, valves, brake pumps, extruding holes, oil fields, laboratories, hydrochloric acid hardness measuring instruments, fishing gear, weights, decorations, finishing in the high-tech industry.
"Jintai" Carbide Strips Advantages
I.Control of Raw Materials:
1.Conducting metallographic analysis to ensure that the WC particle size fluctuates within a certain range, while rigorously controlling the total carbon.
2.Performing ball milling tests on each batch of purchased WC, fully understanding its physical properties, analyzing fundamental data such as hardness, bending strength, cobalt magnetism, coercive magnetic force, density, etc., to comprehend its characteristics.
II. Manufacturing Process Control:
Hard alloy production mainly involves three major processes:
1.Ball milling and mixing, determining the granulation process that decides the loose packing ratio and flowability of the mixture. The company employs highly advanced spray granulation equipment.
2.Pressing and forming, the process of product shaping. The company utilizes automatic presses or TPA presses to minimize human factors' impact on compacting.
3.Sintering, adopting low-pressure sintering technology to ensure uniform furnace atmosphere. The heating, holding, cooling, and carbon balance are automatically controlled during sintering.
III. Product Testing:
1.Flat grinding of carbide strips, followed by sandblasting to expose any uneven density or defective products.
2.Conducting metallographic testing to ensure a uniform internal structure.
3.Performing tests and analysis of physical and technical parameters, including hardness, strength, cobalt magnetism, magnetic force, and other technical indicators, meeting the usage requirements corresponding to the grade.
IV. Product Features:
1.Stable inherent quality performance, high dimensional accuracy, easy to weld, excellent comprehensive performance, versatile for processing solid wood, MDF, gray iron casting, cold-hard cast iron, stainless steel, non-ferrous metals, and other materials.
2.Outstanding intrinsic hardness, high hardness, excellent wear resistance, high elastic modulus, high compressive strength, good chemical stability (resistant to acid, alkali, and high-temperature oxidation), relatively low impact toughness, low expansion coefficient, and characteristics similar to iron and its alloys in terms of thermal and electrical conductivity.
Our tungsten carbide rods are used in a wide variety of precision engineering applications. These strips are used in a variety of industries including manufacturing, machining and tooling. Our tungsten carbide rods offer impressive hardness, wear resistance and strength, making them ideal for precision cutting tools, drills and wear parts. Whether implementing complex design requirements or meeting stringent quality standards, our tungsten carbide rods provide the precision and reliability necessary.
Our commitment to advanced automated manufacturing ensures continuous improvement in quality and efficiency. With their impressive properties, our tungsten carbide rods are perfect for precision cutting tools, drill bits and wear parts. Experience the precision, durability and reliability of our tungsten carbide rods for unrivaled performance in precision engineering.


When it comes to high-quality tungsten carbide strips for your cross-border e-commerce needs, look no further! Our premium tungsten carbide strips are the ideal solution for various industrial applications, guaranteeing top-notch performance and unmatched durability.
Crafted with precision and expertise, our tungsten carbide strips boast exceptional hardness and wear resistance, making them ideal for cutting, shaping, and machining even the toughest materials. From metalworking to woodworking, our strips provide unmatched reliability, helping you achieve precise and flawless results in your projects.
Not only are our tungsten carbide strips built to last, but they also offer excellent heat resistance, ensuring stable performance even under extreme conditions. Count on them to withstand high temperatures and maintain their cutting edge, maximizing productivity and reducing downtime.
At JINTAI, we take pride in delivering products that meet the highest standards of quality. Our tungsten carbide strips undergo rigorous testing to ensure consistency and performance, giving you the confidence to tackle any challenging task with ease.
Upgrade your industrial processes with our top-of-the-line tungsten carbide strips and experience the difference they can make in enhancing efficiency and reducing operational costs. Partner with us today and gain a competitive edge in your industry.
Choose JINTAI for reliable, high-performance tungsten carbide strips, and let us empower your business for success. Place your order now and see the transformative impact of our premium products in action.

Grade List
Grade | ISO Code | Physical Mechanical Properties (≥) | Application | ||
Density g/cm3 |
Hardness(HRA) | T.R.S N/mm2 |
|||
YG3X | K05 | 15.0-15.4 | ≥91.5 | ≥1180 | Suitable for precision machining of cast iron and non-ferrous metals. |
YG3 | K05 | 15.0-15.4 | ≥90.5 | ≥1180 | |
YG6X | K10 | 14.8-15.1 | ≥91 | ≥1420 | Suitable for precision machining and semi-finishing of cast iron and non-ferrous metals, as well as for processing of manganese steel and quenched steel. |
YG6A | K10 | 14.7-15.1 | ≥91.5 | ≥1370 | |
YG6 | K20 | 14.7-15.1 | ≥89.5 | ≥1520 | Suitable for semi-finishing and rough machining of cast iron and light alloys, and can also be used for rough machining of cast iron and low alloy steel. |
YG8N | K20 | 14.5-14.9 | ≥89.5 | ≥1500 | |
YG8 | K20 | 14.6-14.9 | ≥89 | ≥1670 | |
YG8C | K30 | 14.5-14.9 | ≥88 | ≥1710 | Suitable for inlaying rotary impact rock drilling and rotary impact rock drilling bits. |
YG11C | K40 | 14.0-14.4 | ≥86.5 | ≥2060 | Suitable for inlaying chisel-shaped or conical teeth bits for heavy-duty rock drilling machines to tackle hard rock formations. |
YG15 | K30 | 13.9-14.2 | ≥86.5 | ≥2020 | Suitable for tensile testing of steel bars and steel pipes under high compression ratios. |
YG20 | K30 | 13.4-13.8 | ≥85 | ≥2450 | Suitable for making stamping dies. |
YG20C | K40 | 13.4-13.8 | ≥82 | ≥2260 | Suitable for making cold stamping and cold pressing dies for industries such as standard parts, bearings, tools, etc. |
YW1 | M10 | 12.7-13.5 | ≥91.5 | ≥1180 | Suitable for precision machining and semi-finishing of stainless steel and general alloy steel. |
YW2 | M20 | 12.5-13.2 | ≥90.5 | ≥1350 | Suitable for semi-finishing of stainless steel and low alloy steel. |
YS8 | M05 | 13.9-14.2 | ≥92.5 | ≥1620 | Suitable for precision machining of iron-based, nickel-based high-temperature alloys, and high-strength steel. |
YT5 | P30 | 12.5-13.2 | ≥89.5 | ≥1430 | Suitable for heavy-duty cutting of steel and cast iron. |
YT15 | P10 | 11.1-11.6 | ≥91 | ≥1180 | Suitable for precision machining and semi-finishing of steel and cast iron. |
YT14 | P20 | 11.2-11.8 | ≥90.5 | ≥1270 | Suitable for precision machining and semi-finishing of steel and cast iron, with moderate feed rate. YS25 is specially designed for milling operations on steel and cast iron. |
YC45 | P40/P50 | 12.5-12.9 | ≥90 | ≥2000 | Suitable for heavy-duty cutting tools, providing excellent results in rough turning of castings and various steel forgings. |
YK20 | K20 | 14.3-14.6 | ≥86 | ≥2250 | Suitable for inlaying rotary impact rock drilling bits and drilling in hard and relatively hard rock formations. |
Order Process

Production Process
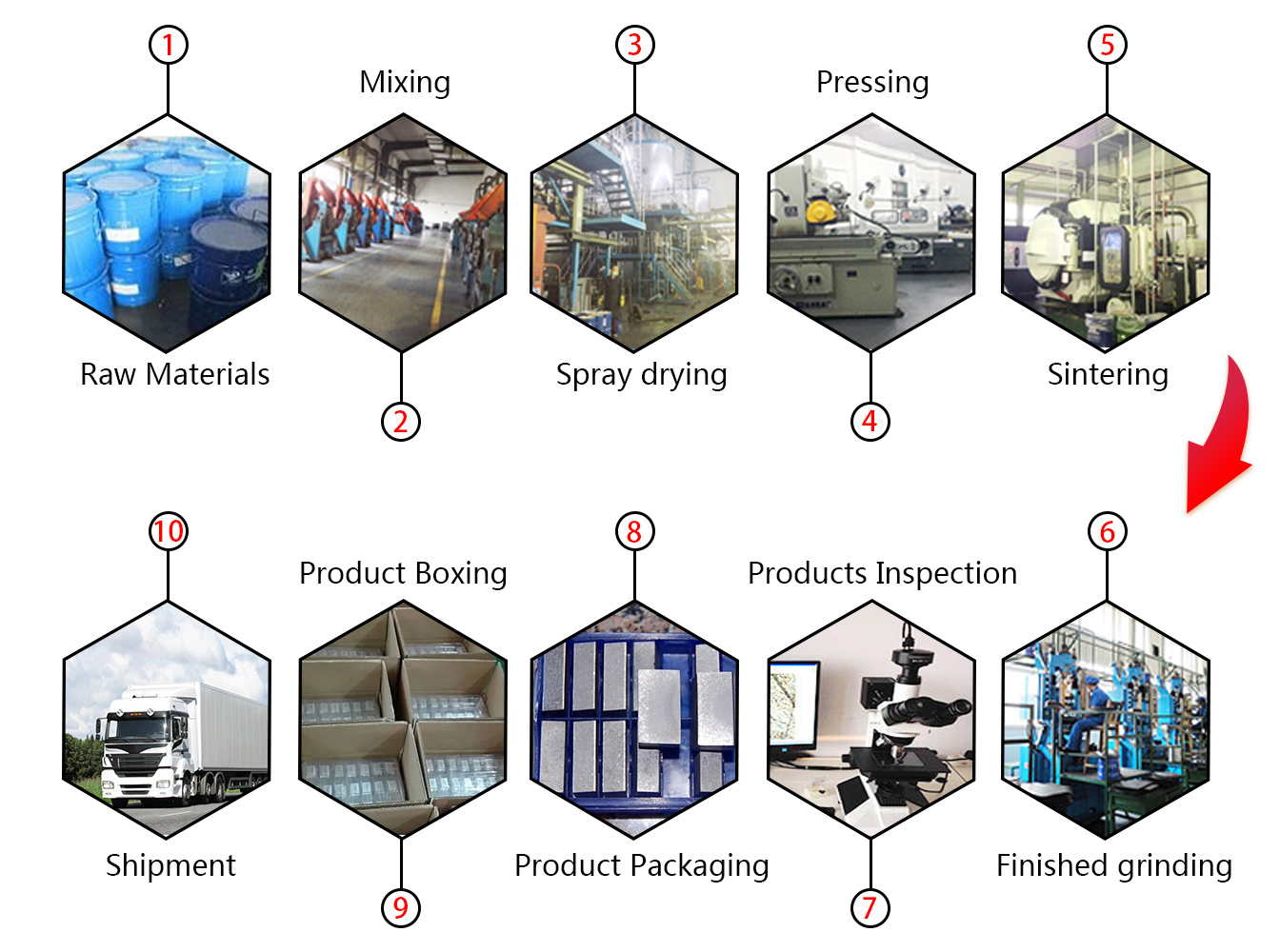
Packaging
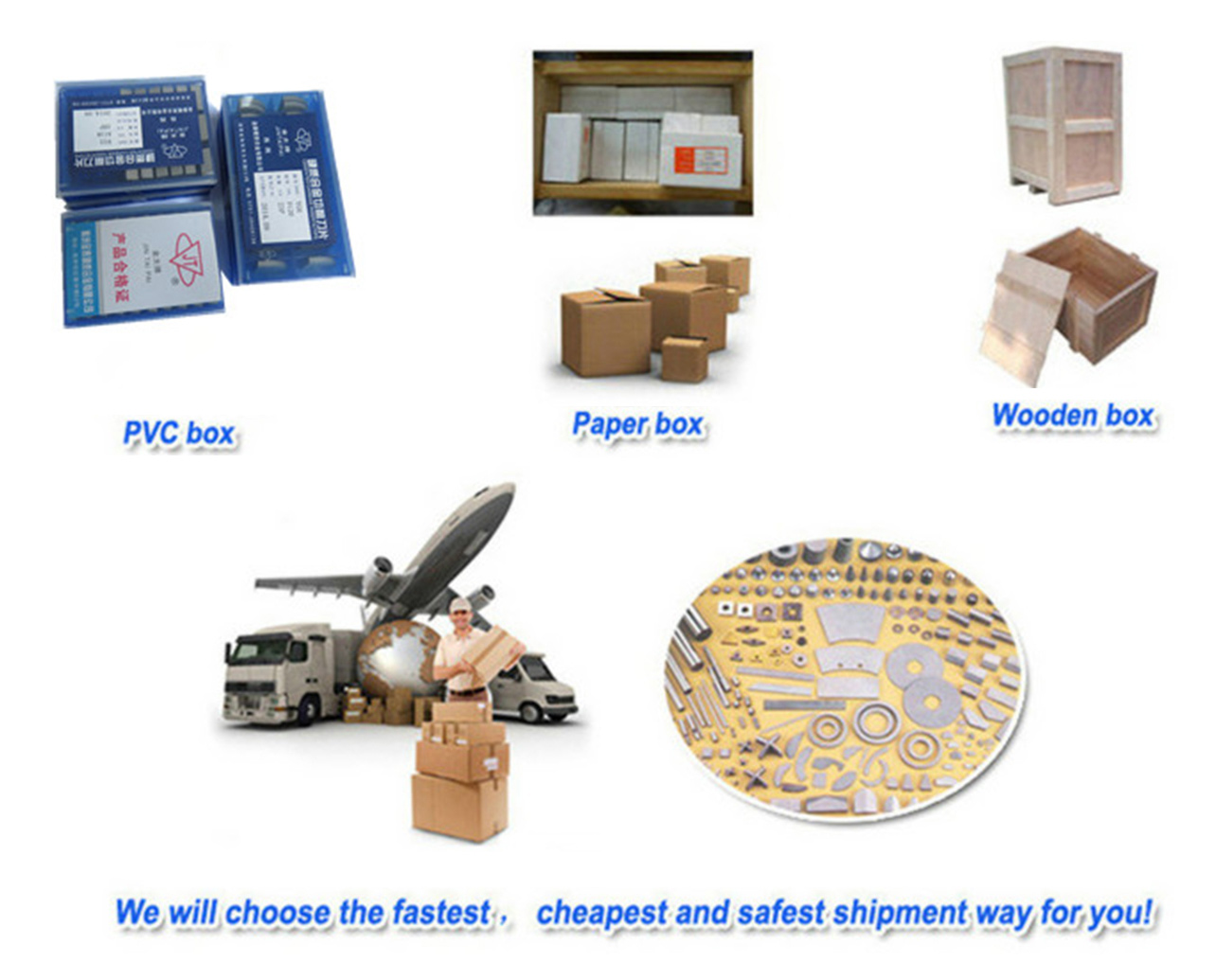